解決事例
CASE 04
銅管の内径を広げる工法転換
after
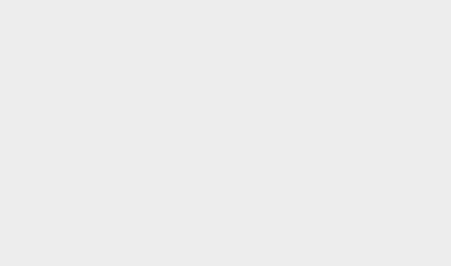
外径を変更せず内径を切削するとなると、面粗度や端面のバリ発生の可能性があることを指摘。そこで、銅管の一部を膨らませる事で面粗度を保ちバリがでない、金型プレスによる工法転換をご提案しました。品質・仕上がり精度が一定に保たれお客様の作業性の向上にも繋がりました。
CASE 03
真鍮部を減らしコスト削減
before
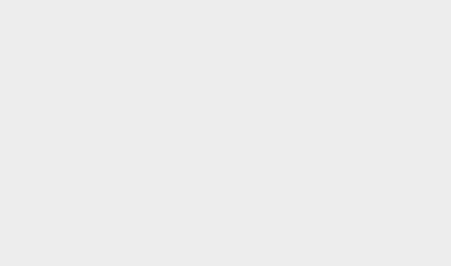
ガス給湯器部品の切削部品の加工にて、従来の金具にロウ付けを行っていた。
コスト削減に繋がる方法はないかと相談されました。
after
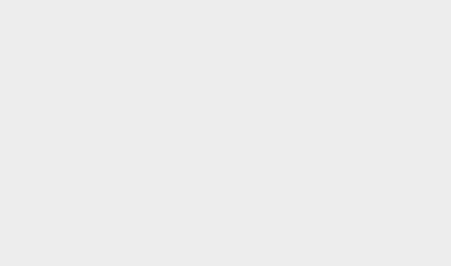
直接パイプに金具をかしめる方法を採用し、真鍮部品の容量を減少させ、ロウ付け工程を削減することをご提案。同時に、形状の検討も必要となる為、図面を新たに作成しました。結果、形状の縮小化ならびに加工コストの削減に繋がりました。
CASE 02
工程短縮によるコストダウン
before
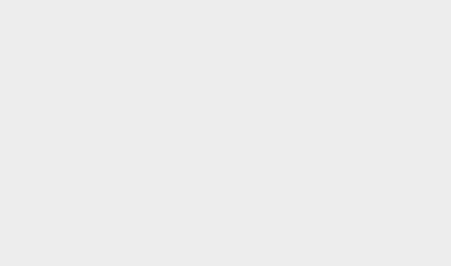
システムキッチン用の部品加工の依頼でした。当初は、両方の先端を片側ずつ加工しなければならず、加工後にパイプの傾きによる不具合が発生するなど、課題がありました。
after
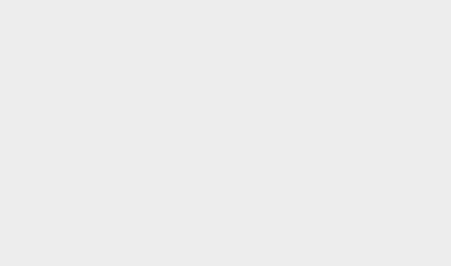
チルトチャックという治具を採用することで、同軸加工が可能。
同時に、加工の工程を1工程に集約することで、曲げ加工時の不具合も解消。人件費・加工費の削減にも繋がりました。
CASE 01
図面無しの加工対応
before
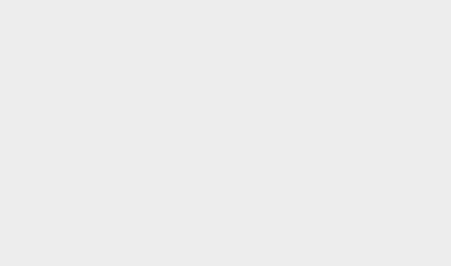
ガス給湯器部品の切削部品の加工にて、従来の金具にロウ付けを行っていた。
コスト削減に繋がる方法はないかと相談されました。
after
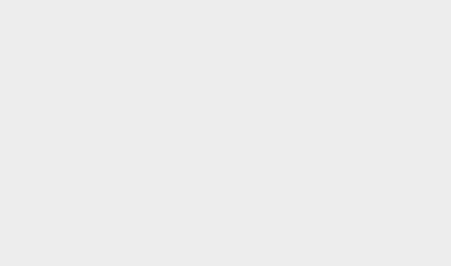
直接パイプに金具をかしめる方法を採用し、真鍮部品の容量を減少させ、ロウ付け工程を削減することをご提案。同時に、形状の検討も必要となる為、右下図のような形状となる図面を新たに作成しました。結果、形状の縮小化ならびに加工コストの削減に繋がりました。